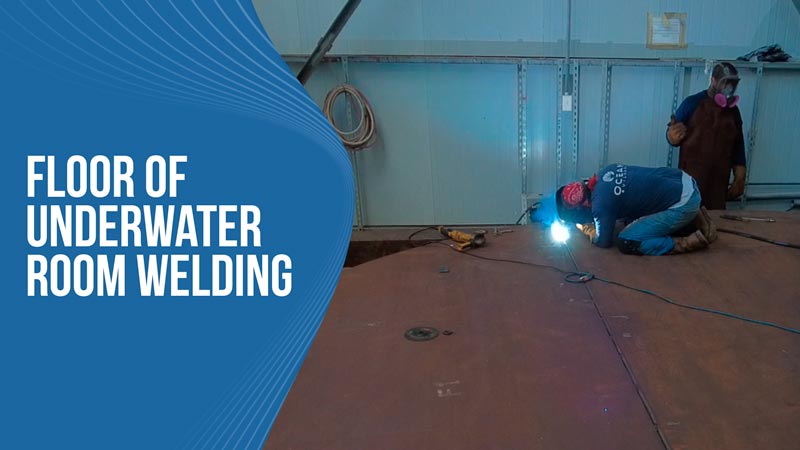
Factory update on the underwater room. Today we’re doing great progress on the floor section.
Thanks to the great work of everyone here who worked so hard to shape these huge and heavy sheets of steel to the right shape so that we can go on with the next part: welding.
As you know, welding is a process that joins two or more pieces of metal by heating the surfaces to their melting point and then applying pressure to fuse them together. There are several different types of welding processes, each with their own advantages and disadvantages.
If it sounds dangerous, it’s because it can be if welders are not protected well enough
We are doing the first of three passes right now. Welding in multiple passes, also known as multi-pass welding, is a technique used to improve the quality and strength of a weld. It is commonly used in thick metal applications where a single pass would not provide enough heat and penetration to properly fuse the metal.
When welding in three passes, the welder typically begins by making a “root pass,” which is the first pass of the weld. This pass is used to establish the initial weld shape and penetration. The welder then makes a “filler pass,” which is used to build up the weld to the desired thickness. Finally, the welder makes a “capping pass,” which is used to smooth out the surface of the weld and improve its appearance.
The benefits of using the multi-pass welding process include:
- Improve the quality of the final weld
- Greater control over the heat input, which can reduce distortion of the metal
- Greater control over the penetration of the weld, which can improve its strength
- Greater control over the weld profile, which can improve its appearance.
It is important to note that the number of passes required will vary depending on the thickness of the metal, the type of metal and the welding process used. Also, the welder should be skilled and experienced in multi-pass welding to ensure the final weld is of high quality. But at Ocean Builders, we of course have the best of welders!