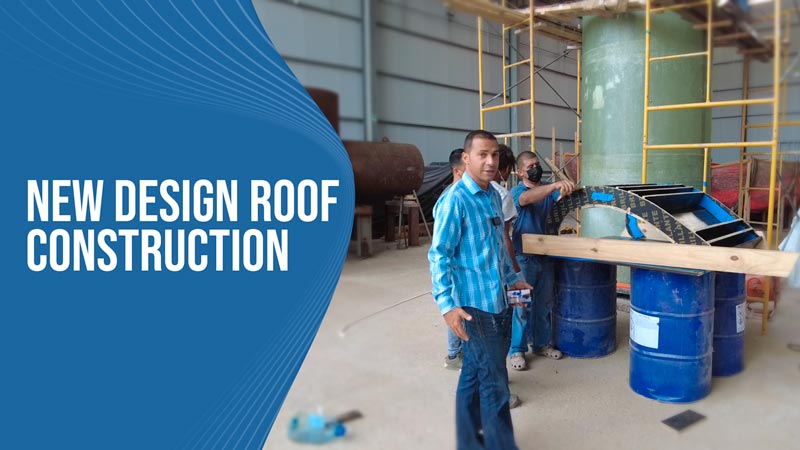
Yesterday we started cutting out the pieces needed for our new roof mold design. This design will be used to make the roof of our Seapod. This Seapod will differ from our flagship design and will be completely round.
In the video, we can see the team working hard to create part of the master plug, which will be used to create a fiberglass mold, which will, in turn, be used to create the roof of this sleek and unique Seapod.
Working with these shapes is painstaking work. Everything must be done manually and measured perfectly for everything to work. The team is measuring the piece every ten centimeters to ensure that the shape and function of the plug will work properly.
Despite the challenges of carefully measuring each section and working manually, the team has made great progress. This piece was only started yesterday and has already come a long way. This really shows the skill and dedication of the team involved that such an important part can be created both quickly but without neglecting accuracy and quality.
At this stage in the design, process accuracy is extremely important, as this will be reflected directly in the mold and then in any pieces created in the mold. If the pieces cast don’t reflect the exact measurements, then the assembly of the Seapod won’t work properly. Of course, working with such important pieces has challenges.
In the video, we can see the team carefully checking their measures. Nothing escapes their attention, and when some of the dimensions present a potential problem, Grant and the team discuss the potential knock-on effects and make a swift plan to get to double-check the dimensions and keep everything moving forward.
We’re excited to keep everyone up to date as this project keeps moving forward, and with the experience and technical know-how of our team, it will continue to move forward steadily.