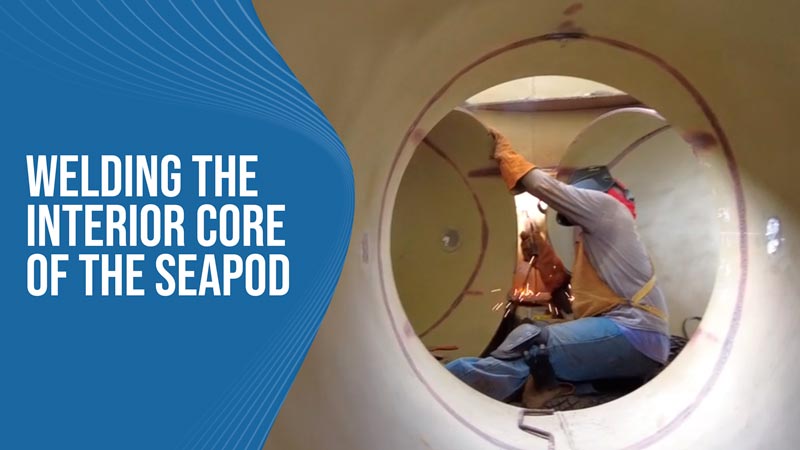
We have been getting quite a bit of work done on our two SeaPod TriPod model bases here at the factory. In this video, we can see one of our welders making some welds on the interior of the core. This is a very important process in terms of giving the base the structural strength that it needs.
The core is where the three outriggers that form the base converge. This is the area that will carry the highest strain and load so we need to ensure that the structure can withstand the stress. The outrigger sections are inserted to the core and welded on both the interior and the exterior.
Another thing that makes these welds so important is that we need this structure to be sealed off from water. These huge steel tubes will actually float and give quite a bit of buoyancy to the whole structure so it is important that they do not fill up with water.
Another cool thing that you can see here is the difference between the surface of the interior and the exterior. The exterior has a thin layer of surface rust so it looks rusty. This is perfectly normal and easily removed, but if left untreated, the rust and corrosion can eat into the structure of the steel.
As you see on the interior, the surface is sort of an off-white color. This is because the interior surface has been sandblasted and sprayed with an epoxy paint that seals the steel and acts as a protectant. The outside will be sandblasted and sprayed with the epoxy paint as well but this is a cool representation that shows the difference between before and after the protectant is applied.
The process of welding all of the sections together is one of the most important parts of building these bases. Thoroughly completing all of the welding on these bases will help ensure that every SeaPod has a sturdy base to float on that won’t leak, fail, or corrode. We are very grateful to have a team of skilled welders helping us to get this project in the water!